You are here:
MIM process: Familiar quality with optimised production
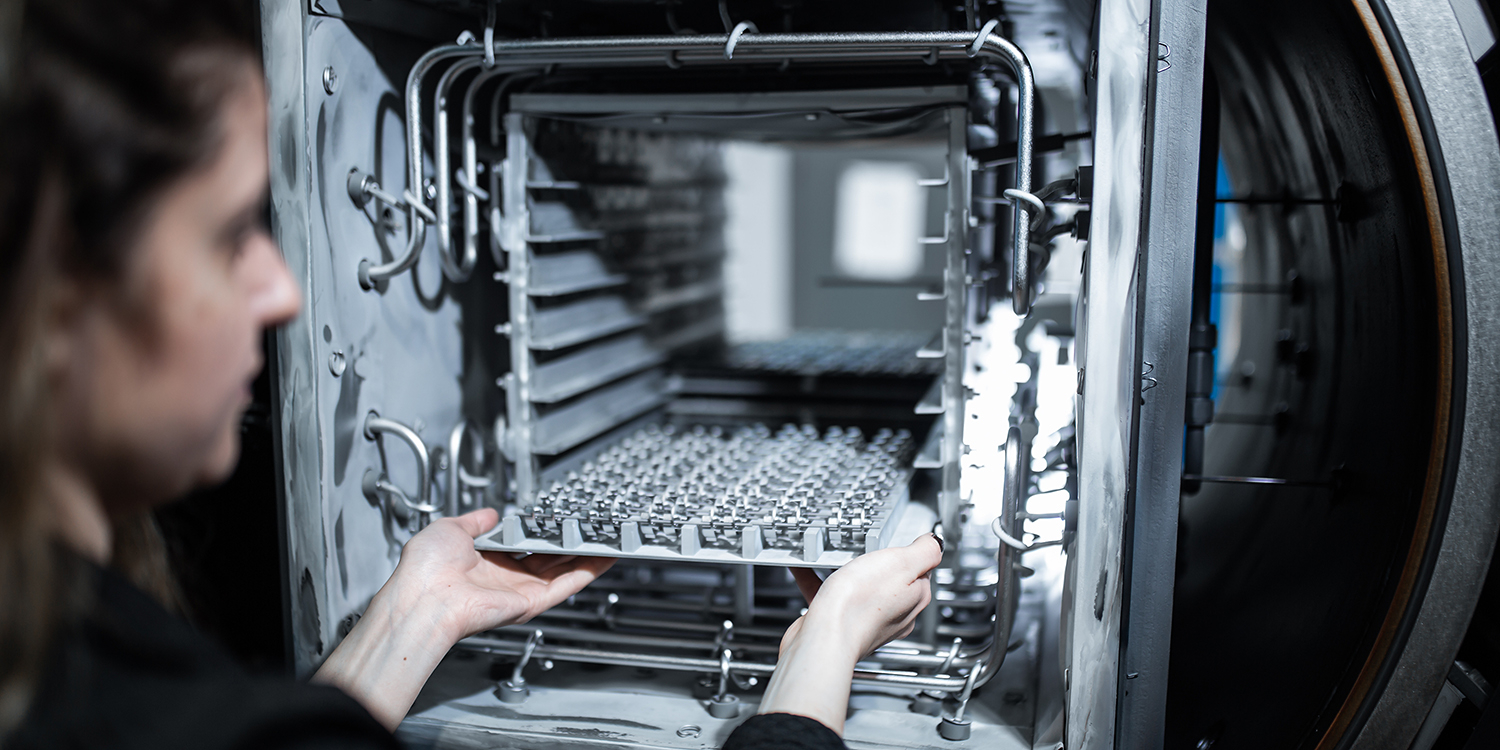
We at REINER® are not afraid to put old methods aside in order to always offer our customers the latest technical standard with our products.
Our design engineers have therefore taken a closer look at the manufacturing process of our stamp wheels.
Our design engineers have therefore taken a closer look at the manufacturing process of our stamp wheels.
“Never change a running system”?
REINER® stamp wheels have always met the highest demands. With success: REINER® products enjoy an excellent reputation in and outside the professional world, not least due to their longevity and outstanding quality.
In the search for optimisation potential, the production of the REINER® stamp wheel was also carefully examined. Until then, the wheel consisted of an inner body made of zinc die casting, an outer body on which the figure wheels were mounted and a fine-blanked part, the ratchet ring, which was riveted to the wheel body. Three processes, each of which was based on a single, tedious production process. Together with the required storage capacity of the components, this caused dissatisfaction among REINER®'s design engineers.
In the search for optimisation potential, the production of the REINER® stamp wheel was also carefully examined. Until then, the wheel consisted of an inner body made of zinc die casting, an outer body on which the figure wheels were mounted and a fine-blanked part, the ratchet ring, which was riveted to the wheel body. Three processes, each of which was based on a single, tedious production process. Together with the required storage capacity of the components, this caused dissatisfaction among REINER®'s design engineers.
The solution: The MIM process!
Since the MIM process (Metal Injection Moulding) has been firmly integrated into the production process, the production of REINER® stamp wheels has not only been massively optimised and made more cost-effective; the quality of the high-quality parts has also been improved. For REINER®, the switch to the process that originated in plastic injection technology has paid off in several aspects.
» You can find even more reasons for the MIM process in precision engineering here.
» You can find even more reasons for the MIM process in precision engineering here.