You are here:
Precision technology from the Black Forest with a special quality promise
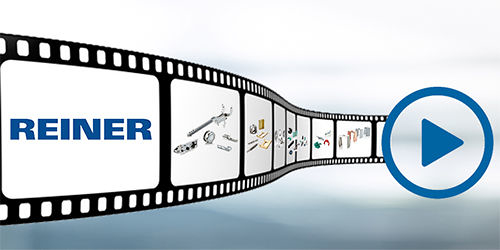
Learn everything about the production options of REINER® precision technology.
Let us present the individual procedure and process steps to you, from innovative design to high-quality parts.
Let us present the individual procedure and process steps to you, from innovative design to high-quality parts.
>>> Learn more in the video on precision technology now
REINER® is your competent contact for production of best precision parts. Many years of experience and comprehensive knowhow guarantee for best quality and highest precision.
Overview of our technologies
• Zinc die-casting
• MIM (metal-injection moulding)
• Fine blanking
>>> Learn more in the video on precision technology now
The advantages of the zinc die-casting process:
The advantages of zinc die-casting are its high strength and the possibility of casting very delicate, thin-walled parts of high technical quality, making this process highly interesting - not only technically but also economically.
Zinc die-cast parts with a part weight of up to 700 grams can be cast with our state-of-the-art die-casting machines and a closing pressure of 5 to 125 tons.
We specialise in small and medium-sized batches. Our dedicated tool making and state-of-the-art zinc die-casting machines ensure an outstanding result at all times.
REINER® components achieve the highest precision here.
This equally applies to zinc die-cast parts and to parts we produce for you with the MIM process.
Zinc die-cast parts with a part weight of up to 700 grams can be cast with our state-of-the-art die-casting machines and a closing pressure of 5 to 125 tons.
We specialise in small and medium-sized batches. Our dedicated tool making and state-of-the-art zinc die-casting machines ensure an outstanding result at all times.
REINER® components achieve the highest precision here.
This equally applies to zinc die-cast parts and to parts we produce for you with the MIM process.
Advantages of the MIM – Metal-Injection Moulding – process:
The main advantage of MIM, or metal injection moulding, is in its ability to produce even parts with highly complex geometries. The process is also suitable for integrating bores, grooves, etc. in the production process.
Production of thin-walled parts with very high accuracies is possible as well.
This results in high-quality geometrical parts that can perform challenging functions. We produce parts with sizes of tool clamping surface up to 400 x 700 mm and a part weight of up to 75 g.
Production of thin-walled parts with very high accuracies is possible as well.
This results in high-quality geometrical parts that can perform challenging functions. We produce parts with sizes of tool clamping surface up to 400 x 700 mm and a part weight of up to 75 g.
Which options does REINER® offer in the area of punching?
We offer precision punching, NC punching, NC bending and laser cutting.
Parts with a maximum tool clamping surface of 500 x 500 mm can be punched.
Punching thicknesses of 0.5 mm to 4 mm are possible. A process that matches the requirements posed to the part to be produced will be chosen.
REINER®'s experts will advise you individually regarding the method that is best for your process and for your product.
Parts with a maximum tool clamping surface of 500 x 500 mm can be punched.
Punching thicknesses of 0.5 mm to 4 mm are possible. A process that matches the requirements posed to the part to be produced will be chosen.
REINER®'s experts will advise you individually regarding the method that is best for your process and for your product.
Innovative tool making - everything from a single source
REINER® has a dedicated internal tool design department, employing top specialists with many years of experience. This leads to flexible and quick implementation of individual customer wishes.
We believe that a dedicated tool-making capacity is vital for precise and smooth production of high-tech parts. Therefore, we produce the moulds, precision punching tools and devices we need for the processes in-house exclusively, using state-of-the-art technology.
• Sink and wire erosion
• Flat, profile and jig grinding
• State-of-the-art CNC programming technology
• Precision lathes
• HSC milling
• Coordinate measuring technology for mould and sample measurement
• Centres for machining processing
REINER® precision technology – Precisely shaped ideas
We are looking forward to your request.
We believe that a dedicated tool-making capacity is vital for precise and smooth production of high-tech parts. Therefore, we produce the moulds, precision punching tools and devices we need for the processes in-house exclusively, using state-of-the-art technology.
• Sink and wire erosion
• Flat, profile and jig grinding
• State-of-the-art CNC programming technology
• Precision lathes
• HSC milling
• Coordinate measuring technology for mould and sample measurement
• Centres for machining processing
REINER® precision technology – Precisely shaped ideas
We are looking forward to your request.